The complete conveyor experience
Delivers superior outcomes on site
So performance never stops.
Optimise my site
World-leading conveyor equipment technology
Improve conveyor performance
Accelerating mining globally
Manufacturing conveyor components internationally with local manufacturing facilities in Australia, Brazil, Canada, USA, Indonesia and Chile.
Title
Don’t get left behind
We don’t stop chasing performance, and neither should you. Optimise your site today.
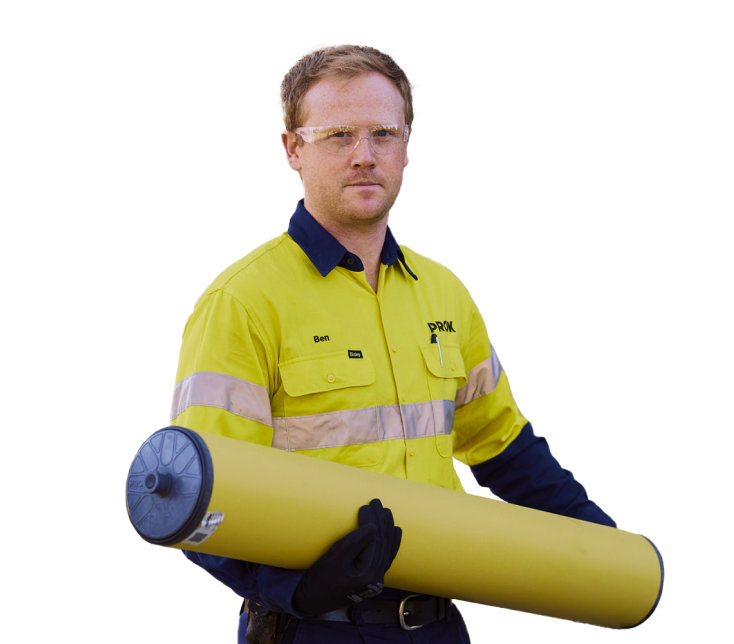